Electronic waste (e-waste) is a growing problem, with a record 62 million tonnes (Mt) of it being generated worldwide in 2022.
At the same time, there is a growing demand for critical raw materials (CRMs), including rare metals, to sustain the rapid growth of existing and emerging technologies.

Recycling as much metal as possible from e-waste plays a crucial role in mitigating shortages of critical metals, as well as reducing the need for damaging mining operations.
There are a number of drawbacks to current metal recycling techniques, however.
Hydrometallurgy – a process that uses liquids to first dissolve and then reclaim the metals – involves substantial water and chemical consumption, and also produces secondary waste streams.
Existing heat-based pyrometallurgy, meanwhile, lacks selectivity and requires substantial energy input.
Now, researchers in Texas have detailed a newly developed technique that they say is able to recycle metals from e-waste more efficiently and with reduced environmental impact.
The new technique uses flash heating and chlorination, an industrial process that involves reacting chlorine and oxygen with specific metals in a mixture.
While still reliant on heat and additional chemicals, it allows both to be deployed in a more controlled manner.
Flash Joule heating uses electric current to produce high temperatures
The technique, detailed in the journal Nature Chemical Engineering, is built on a method known as flash Joule heating (FJH) that lead researcher Professor James Tour had previously used in waste disposal.
FJH involves passing an electric current through a material to rapidly heat it to extremely high temperatures, transforming it into different substances.
It enabled extremely fast and precise levels of heat to be applied to the e-waste, allowing the team to successfully recover a number of different metals.
Tests saw the team effectively separating tantalum from used capacitors, gallium from discarded light-emitting diodes (LEDs), and indium from used solar conductive films.
The precise control over reaction conditions provided by the technique allowed the team to achieve a metal purity of more than 95% and a yield of over 85%.
The researchers now intend to adapt the process to recover other critical metals from waste streams and believe that their method holds promise for extracting lithium, a crucial ingredient in many battery technologies.
It could also potentially be used on other industrial waste and even crude ores from mining.
Today’s news was brought to you by TD SYNNEX – the UK’s number one solutions distributor.
Sustainability
We’re focused on meeting the demands of the present without compromising the needs of future generations.
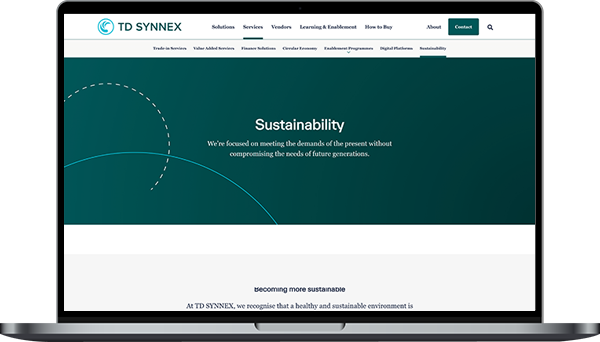
Read more of our latest Sustainability stories